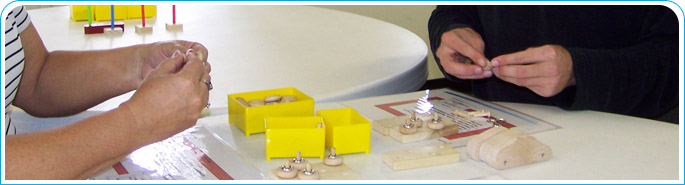

Lean Enterprise Training
In today's unprecedented business environment, we are facing constant pressures resulting from our global economy and customer demands are increasingly more demanding. Lean Enterprise methodologies can help you to remain competitive, innovative and profitable. Implementing "Lean" can reduce your cycle time, minimize inventories, improve customer satisfaction, gain employee buy-in, all of which will help improve your bottom-line.
We deliver proven, practical and leading edge training for Lean principles and practices so your organization can achieve dramatic results. We know adults learn best by "doing" and our Lean Enterprise Training uses numerous simulators to stimulate and expedite the learning experience and foster team interaction and development. Our training is more hands-on than traditional seminar-type training and it is customizable to your organization. We come to you and we provide all of the simulators and training media. Our field experienced instructors will provide your team with the building blocks of the "house of lean" that will help you achieve dramatic results for you and your team.
Our Lean Enterprise training delivers a wide range of methodologies:
- We specialize in the building block methodologies of a Lean organization including 5S, change management, visual systems, plant layout, quality at the source, teamwork, Quick Changeover, point-of-use storage, Autonomous Maintenance, push/pull/kanban, Key Performance Indicators, and continuous improvement.
- We train your team to use their "lean glasses" to see the wastes of overproduction, motion, conveyance, waiting, over-processing, and underutilized and uninvolved people using our unique and highly interactive 5S Simulation, The Lean Car Factory Simulation, and The Ultimate Lean Simulator.
- We demonstrate how to analyze the gap you have between what you are currently doing and that of best in class. Then, demonstrate a method to develop critical company-wide goals, key performance indicators to help you measure success, and implement an action plan to achieve the goals that focuses on accountability, achieving tasks and team involvement. Our experience has shown that, with proper management, typically over ninety percent of the KPI's improve over 10% within the first 12 months.
- We demonstrate methodologies to make better use of your employees' time and brainpower in a team environment by involving them as Subject Matter Experts (SME's). They will interact throughout the Lean Enterprise Training in teams using the Ultimate Lean Simulator on the first day and throughout the course, they will go through a multiple step 5S simulation that uses all of the 5S steps, and they will operate their own car manufacturing assembly plant to learn the principles of Lean and, as the course finale, they will put their new knowledge into practice using the Ultimate Lean Simulator to deliver a team project of the key Lean fundamentals.
- We demonstrate a great employee suggestion process that is dynamic and based on actionable items with consistent feedback.
Delivery Method: Classroom, interactive simulations, participative class interaction and teamwork
Audience: Our training is designed to educate all levels of an organization. All employees benefit from the interaction and participation.
Cost and Scheduling: Contact us and we will customize a plan for you.
Request more information
Are you interested in learning more about our unique approach to teaching Lean Manufacturing and Lean Office principles to your employees? Fill out our assessment form and tell us how you'd like to improve or contact us today for more information.