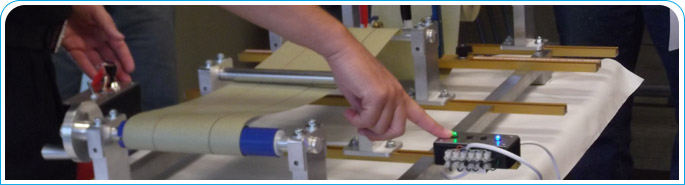

Quick Changeover
There are five primary reasons an organization should seriously devote resources to reduce the time it takes to make changeovers, they are: reduced changeover times, improved quality, increased productivity, reduce costs and finally, it makes the job easier. In these difficult economic times it would be very prudent for companies that perform changeovers to dramatically reduce their current changeover times.
Hands on learning with the QCO/Ultimate Lean Simulator
We will provide your management staff and operators with the fundamentals and science of the Quick Changeover process. Next, using our Ultimate Lean Simulator, we will demonstrate some of the issues traditionally faced. Time is allowed for the group to develop, implement and demonstrate what changes they made to reduce the original changeover time. Typically students have demonstrated between 50 to 93% reduction in the established simulated changeover time. Having operators included in this training is an excellent way to obtain buy-in and give operators a sense of ownership. This inclusionary method allows managers to relay expectations to operators in a non-threatening enjoyable environment. Operators will also understand management's perspective and they will understand the importance of the new task being asked of them. When operators are given the opportunity to succeed they will certainly step up to the challenge.
Flexible programs for implementation
The use of the Ultimate Lean Simulator for Quick Changeover training only, does not include the complete course syllabus as outlined in Lean Enterprise Training. This training is typically a half day session. However, with proper scheduling a two day session would include the half day training followed by documenting your facilities changeover, documentation of delays and follow-up with the same crew who preformed the changeover. Operator improvement suggestions will be presented to management for review and further discussion with operators as in house scheduling permits. If you or your organization believe additional support from our consultant(s) is necessary to fully complete and implement new changeover procedures we can be available to assist you at your site.
Request more information
Are you interested in learning more about our unique approach to teaching Lean Manufacturing and lean office principles to your employees? Contact us today or fill out our assessment form to tell us how you would like to improve your processes and results.