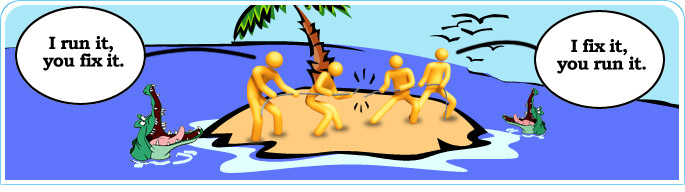

Autonomous Maintenance
Autonomous Maintenance (AM) is a team based approach to reducing equipment failures, improving utilization and reducing maintenance costs. Autonomous Maintenance places a focus on the equipment to ensure basic equipment maintenance is performed properly and in a timely fashion. Autonomous Maintenance is a basic building block to preventing breakdowns and quality problems.
AM methodologies promote team based preventative maintenance
AM prepares operators to perform some basic maintenance activities such as inspections, cleaning and small adjustments. However, they are not on an island by themselves. They are part of a team of operators, engineers, technicians and managers who work together for the good of the machine. Autonomous Maintenance is a process of helping operators' gain knowledge of their machines and developing their ability to recognize abnormal operating conditions. They can then be taught to perform routine checks and minor maintenance tasks while freeing up maintenance personnel for predictive and preventative maintenance.
We provide a two day work shop which includes the identification of the team members, roles and responsibilities are defined, team Equipment Care communication systems are discussed and defined, and an action plan is developed with team assignments.
The course syllabus is as follows:
- Introduction to Autonomous Maintenance
- Team exercise: What Autonomous Maintenance means to you.
- What AM is and is not
- Video
- AM 5S
- Team Charter
- Seven steps to AM
- Beta site definition
- Setting Goals
- Developing Action Steps
During this process we will form teams consisting of maintenance personnel, operators and engineers and technicians. Jointly, the teams will develop operator daily checks, lubrication schedules, and a methodology will be implemented that will allow operators and maintenance personnel to communicate with each other to answer questions, fix nagging problems, install poke yoke (mistake proofing) and help operators identify how to make minor adjustments. This process does not take away the duties of any craftsperson; in fact it enhances their role because they are educating the operators. Nor, does it significantly increase the workload of the operator. It gives them a communication avenue to eliminate the problems that plague them when the “right” person is not around to solve their problems.
Autonomous Maintenance is based on education and training. It is about raising awareness of the operators’ knowledge and understanding of the operating principles of their machines. They will be able to respond quickly to abnormal conditions by having the knowledge to intervene effectively or know where to get help.
A typical implementation will include:
- Management Training and Strategy Development
- Autonomous Maintenance Teams and Areas Defined
- Autonomous Maintenance Teams Trained Including 5S Training
- Team project charter finalized
- Autonomous Maintenance communications system developed
- Beta equipment 5S started
- Autonomous Maintenance assignments defined and developed with teams. Includes both maintenance and operations personnel
Our unique process is interactive on a daily basis, uses visual management boards, has a special communication system that is both manual and PC based and is a practical approach to solving daily maintenance problems. You will be amazed at the results.
Request more information
Are you interested in learning more about our unique approach to teaching lean manufacturing and lean office principles to your employees? Contact us today or fill out our assessment form to tell us how you would like to improve processes and results.