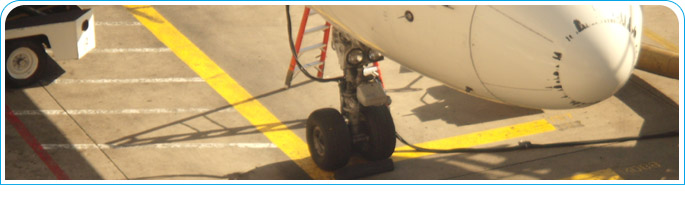

Standardization
A standard is defined as the current best demonstrated practice. Basically, it is the best known method for completing a specific task. Standardization is a cornerstone of the Lean Enterprise and is used as a fundamental building block for continuous improvement by the Toyota Production System.
Learn to Accept the 100% Quality Standard
Business Process Solutions wholly embraces Lean methodologies. We believe the process of developing and adhering to standards is the single most valuable tool an organization can use towards becoming more successful. Consider, for a moment; what quality standard would you accept? Is it 97%, maybe 98%, No? How about 99%? Most companies consider an overall rating of 99.9% to be very good. However, at the 99.9% quality level there would be two long or short landings at American airports each day. Obviously only 100% quality is the only acceptable standard. So, why do we accept anything less then 100 percent? Because, all processes have variation, errors, mistakes and equipment damage is often prevalent. These failures cost us a tremendous amount of time, money, accidents and quality problems that result in unsatisfied customers. Typically, these failures result because standards do not exist and if they do exist they are often outdated or employees have not been properly trained to use the standards.
Standardization results in safety and success
Since 1980 there is only one American airline that has never crashed an airplane. When a pilot for this airline was asked, to what do you attribute this outstanding track record? The reply was literally a one word answer, "standardization." The pilot further added that for every scenario there is a standard to follow and each time new challenges arise everyone participates in the development and testing of a new standard to overcome the challenge. When a pilot has a suggestion for changing an existing standard, as this pilot explained, the company is very open and in fact encourages input from employees. Another outstanding example of how important it is to have strict adherence to good standards is during an emergency. The airline being discussed here is UPS and since they have been flying their own planes (1980) they have only had one major incident when a plane caught fire in the air. By following their standard procedures the crew was able to safely land the plane and evacuate the crew with no injuries.
Assure Quality with the Quality Airplane
Business Process Solutions uses standards as the instruments to train personnel and then if failures occur RCFA can be used to analyze why. Thus, we begin to no longer accept failures as part of the landscape. Additionally, we know that all known methods can be improved; therefore, standards become the basis for continuous improvement.
Developing good standards and consistently adhering to them will produce many benefits:
- Reduces variation which interprets into improved quality and customer satisfaction
- Uses employees as “Subject Mater Experts” (SME’s) to participate in developing the current best demonstrated practice which results in greater buy-in.
- Provides the basis for training and failure analysis
- Provides greater organizational accountability
- Reduces downtime and equipment failures.
We provide a methodology to help organizations define critical processes and develop standards using their SME’s to capture the current best demonstrated practices. These are then placed in a proprietary pictorial format for ease of training. The process is then used as the basis of Failure Analysis and continuous improvement.
Request more information
Are you interested in learning more about our unique approach to teaching lean manufacturing and lean office principles to your employees? Contact us today or fill out our assessment form to tell us how you would like to improve processes and results.