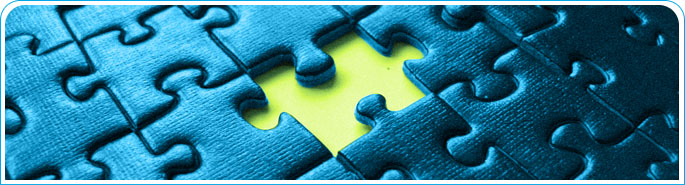

Problem Solving
The best way of solving problems is not to call them “Problems”, but to take a new approach called appreciative inquiry. This approach states that “problems or issues” can be a result of our own perspective, as it pertains to an event. In other words, if we look at something as a problem or an issue then it will become one, and we will probably become stuck on the problem.
Business Process Solutions utilizes several problem solving techniques that follow the appreciative inquiry scheme. Many of these techniques are demonstrated in the Lean Enterprise Training session. Often these problem solving tools are underutilized, thought to be understood but really are misunderstood, or turn into complaint sessions where problems still remain problems. By having students physically demonstrate the use of several different techniques through-out the course they gain a complete practical knowledge of how to apply them in actual settings.
Some of the “problem solving” tools used are:
- Root Cause Failure Analysis
- Quality Improvement Story
- Situation Target Proposal
- Brainstorming
- 5-Why Analysis
- Affinity Diagrams
The complete understanding and proper use of these problem solving techniques play a key roll in the development of standards necessary to achieve 100 percent quality. Students who participate in our Lean Enterprise Training are presented with actual scenarios and will use several different appreciative inquiry techniques to identify the root cause and eliminate the problem. Students will then have the knowledge to utilize these methods at there work site with confidence.
Request more information
Are you interested in learning more about our unique approach to teaching lean manufacturing and lean office principles to your employees? Contact us today or fill out our assessment form to tell us how you would like to improve processes and results.